General Manager Damien Sauni needed a partner to build a fully custom Rollforming machine — one that could manage the high output of a diverse product offering, with minimal operator intervention. After a long relationship of 40 years, Hayes International was, in Damien’s eyes, the best partner for the job.
Rafted Rollformer Standard Components Details
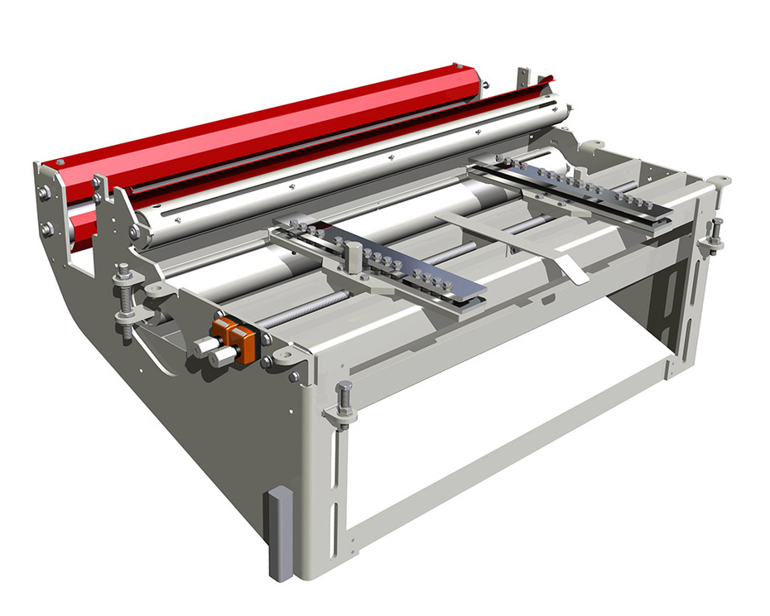
- Adjustable infeed guides to suit coil discrepancies and control under/overlap length; positioned via Siko type screw adjustment.
- Built in lubrication system with felt wick applicator that applies lubricant to both sides of the sheet.
- Manually operated hand slitter with D2 hardened steel knives to reduce waste material.
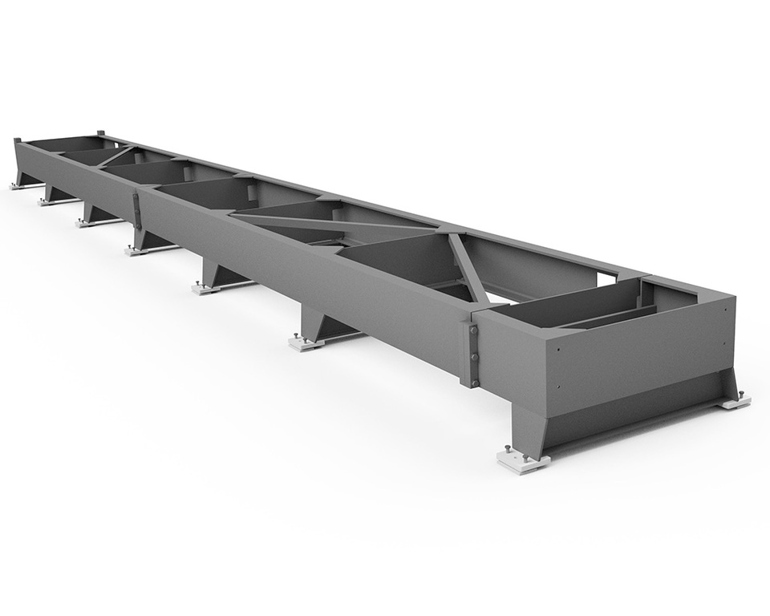
-
Fabricated steel chassis in segments for easy handling, painted with a lacquer finish.
-
Reference marking and leveling feet for ease of alignment.
-
Locating pins make aligning rafts onto the chassis easy.

-
Welded steel design with a lacquer paint finish, manufactured in segments to allow changeover without heavy lifting equipment.
-
Pedestals are a heavy-duty welded steel design with all working surfaces precision machined.
-
Each pedestal houses heavy-duty self-aligning bearings with tooling shaft locking collars.

-
Precision CNC Machined.
-
K1045 grade solid steel with hard chrome finish.
-
2-inch diameter main tooling journals.
-
Corrective passes to adjust cover width and adjustable side tooling dependent on profile.
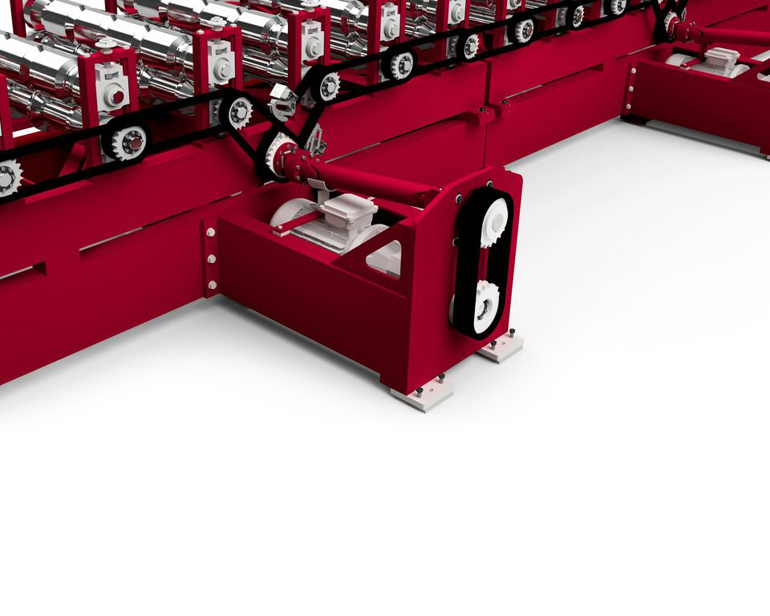
-
Driven by dedicated VFD Electric motor mounted externally via driveshaft and constant velocity joints.
-
Power transmitted via heavy duty chain and sprocket.
-
Secured via Bonfix style couplings.
-
Each bottom roll of tooling is driven, with the first stations coupled via spur gear to aid traction.
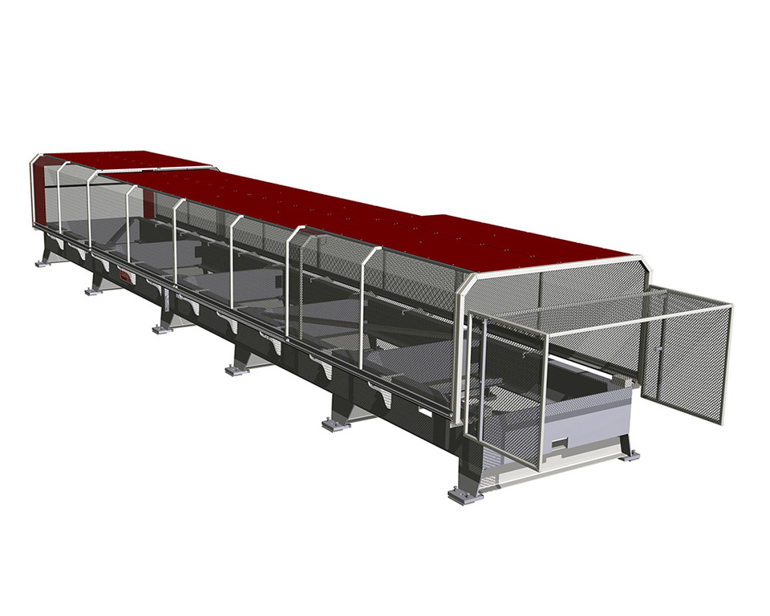
- Guarding covers tooling rolls and transmission.
- Welded steel and mesh construction painted with lacquer finish.
- 2 Configurations available: 'Lift up' guards that open upwards with the aid of gas struts or interlocking tunnel guards that open via sliding on track and rail system.
- All guards are equipped with interlocking safety switches integrated into the safety system.
- Polycarbonate guarding option available.
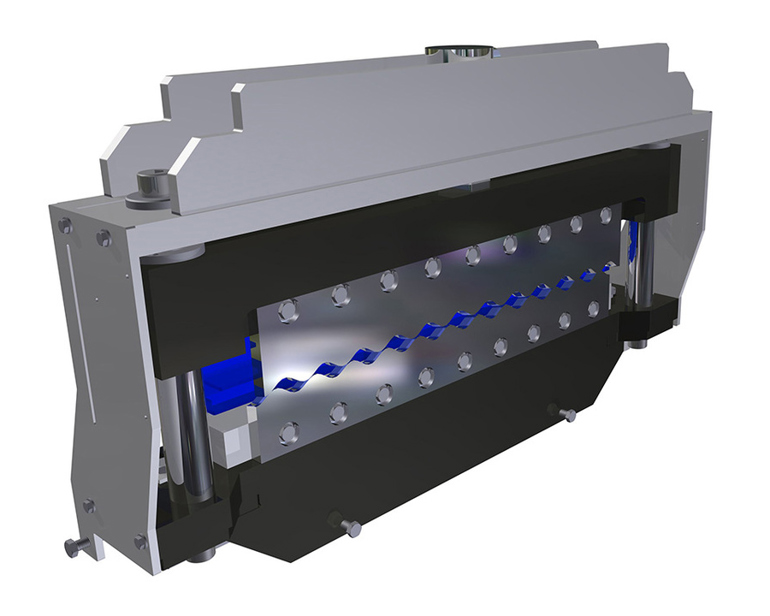
- Heavy duty twin pillar post-cut guillotine.
- Hydraulically operated via a dedicated power pack.
- Replaceable D2 through-hardened steel blades that are precision ground and sharpened.
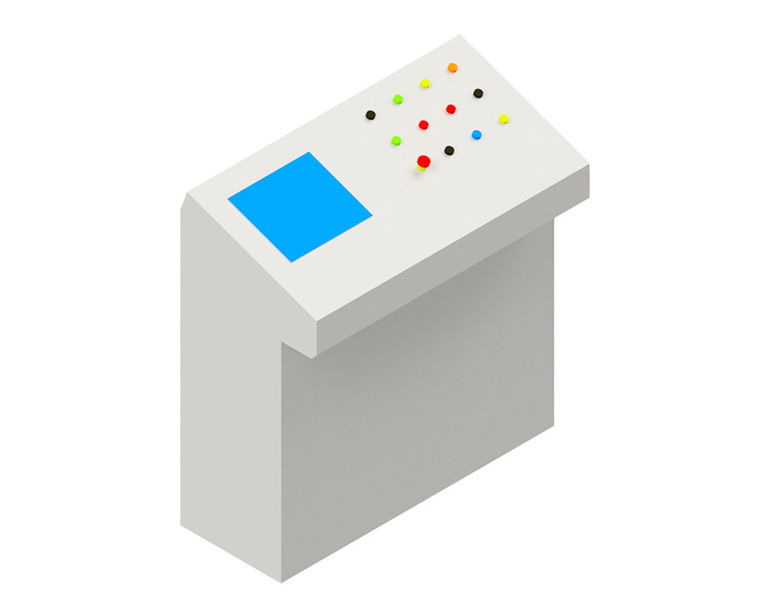
- Dedicated operator console controlled via a PC and Hayes SmartCut multi batching control.
- Fully instrumented controls capable of operating in manual or automatic modes.
- Data download and order entry facilities, as well as fault-finding capability and operating safety system.
- Can be configured to run select 3rd party control systems.
- ERP integration capability (subject to controller type) with production reporting, scrap monitoring, etc.
Request A Quote
If you’re ready to take the next step, let us know below. One of our team can get in touch to talk through your project. If you’d like to share a drawing, attach it below. We look forward to receiving your enquiry.