General Manager Damien Sauni needed a partner to build a fully custom Rollforming machine — one that could manage the high output of a diverse product offering, with minimal operator intervention. After a long relationship of 40 years, Hayes International was, in Damien’s eyes, the best partner for the job.
'Quick Change' Purlin Standard Components Details
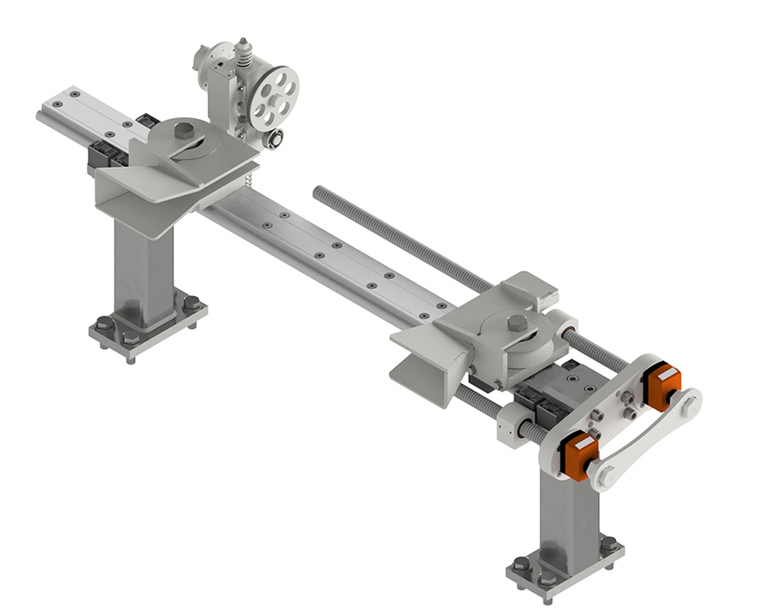
- Adjustable Vee throated infeed guides to suit coil discrepancies positioned via Siko-type screw adjustment.
- Primary strip feed rolls machined from hardened 4340 steel rolls spur gear coupled and fitted with chain-coupled pressure screws to adjust traction.
- Straightening rolls to remove 'coil set'.
- Recycling spray lubricator applies lubricant to both sides of the coil before forming process.
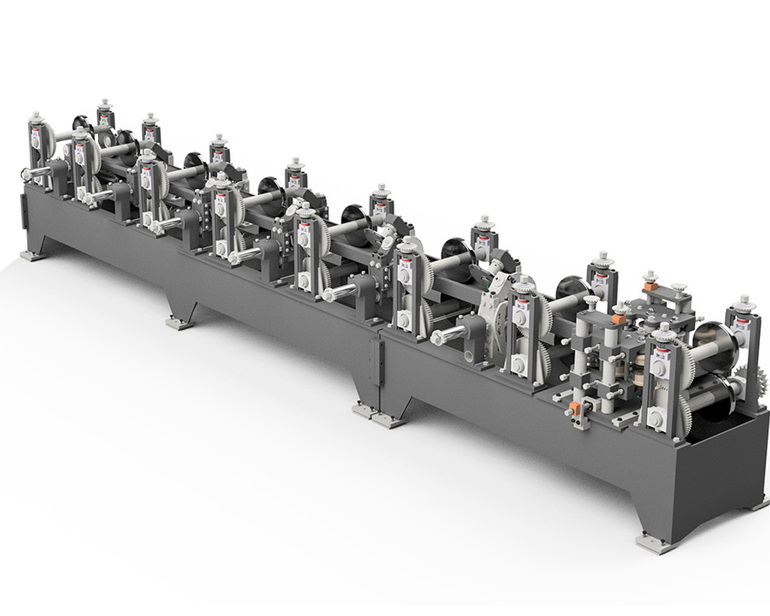
- Fabricated steel chassis manufactured in segments for easy handling and painted with a lacquer finish.
- Reference marking and leveling feet for ease of alignment.
- Pedestals are prefabricated welded steel designs with all working surfaces precision machined.
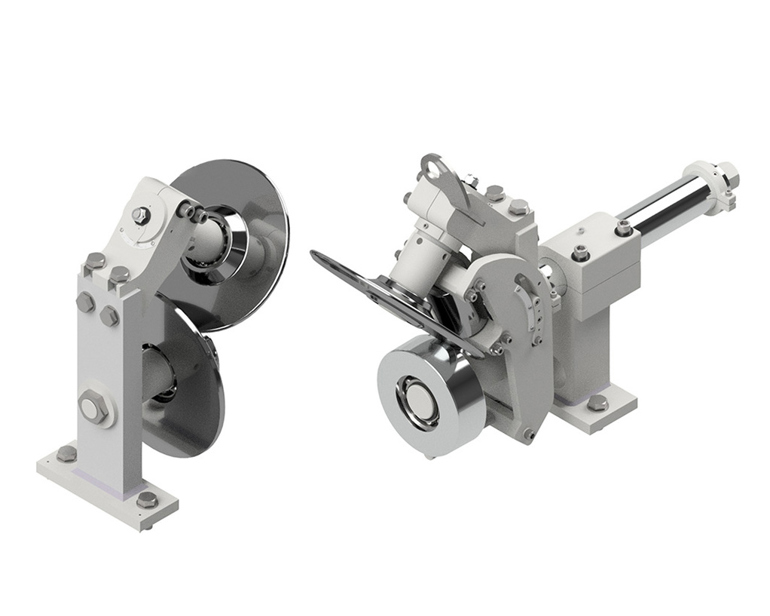
- The Hayes 'Quick Change' system allows for quick changeover from Cee to Zed Purlins.
- Changeover tooling is mounted on a chrome bar that can be rotated 180 degrees for Cee to Zed changeover and moved inwards or outwards to achieve the correct web thickness.
- No special tools are required, and setting gauges are included for common web sizes for even faster changeover.
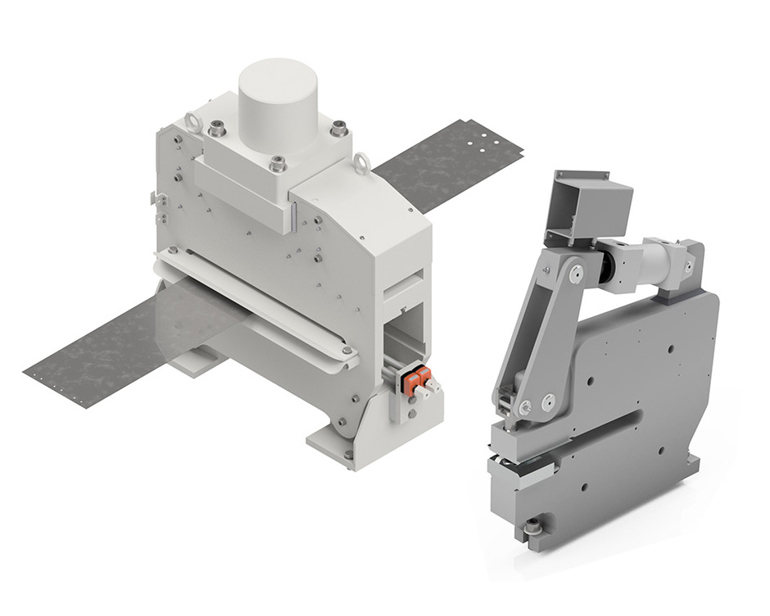
- Hydraulically powered via a dedicated power pack.
- Static shear for trimming coil lengths and interchangeable part-cut die that leaves a small amount of material between profiles that can be easily snapped for lengths below 1750mm.
- Dynamic punch heads are positioned on moveable rafts to adjust the hole position, and the punch head amount is configurable depending on production requirements.
- The amount of punch heads are configurable based on production requirements.
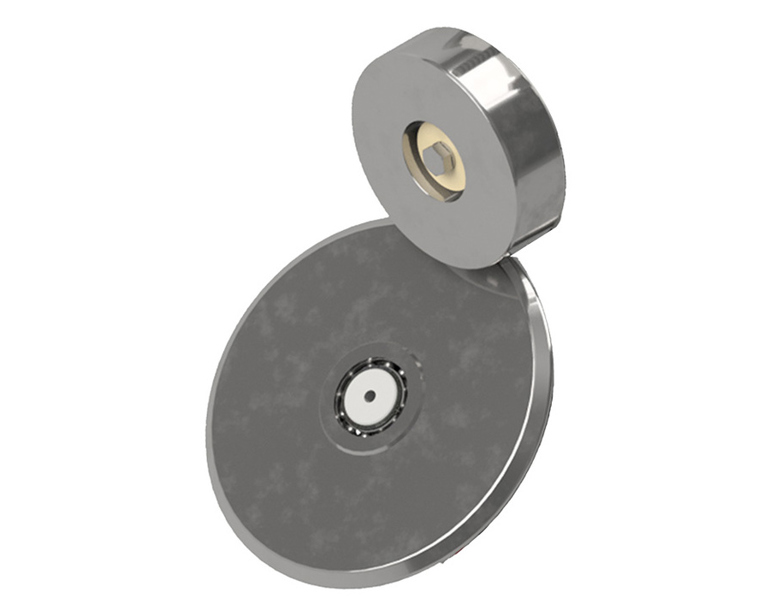
- Solid D2 steel tooling rolls precision CNC machined and through-hardened to RC60 grade.
- Tooling stations are manually gauged against reference marks.
- Standard tooling equipped for Cee and Zed purlins. Optional tooling sets are available for sloping eaves and sigma purlins.
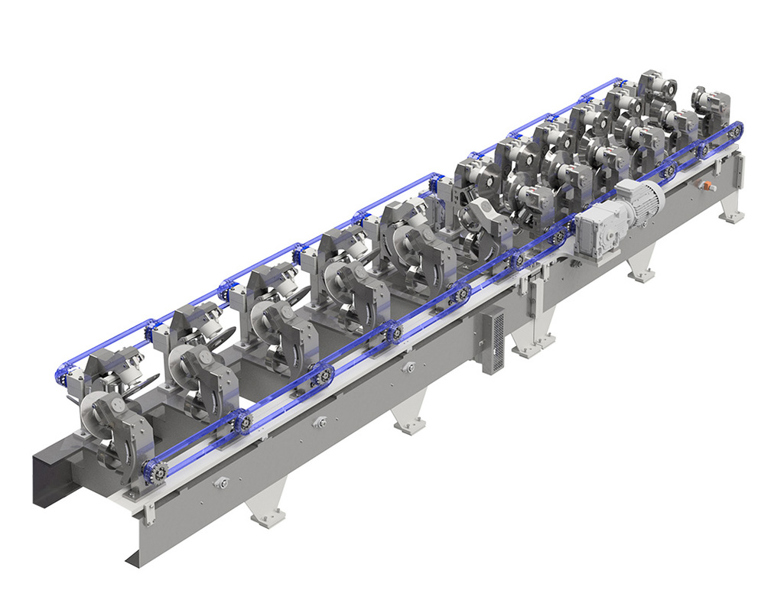
- AC Electric gear motors coupled via chain and sprocket transmission drive the main tooling rolls.
- Drive motors controlled via a VFD for accurate strip positioning and smooth stop-to-cut operation.
- Pinch feed rolls are powered by dedicated motors and coupled via spur gear.
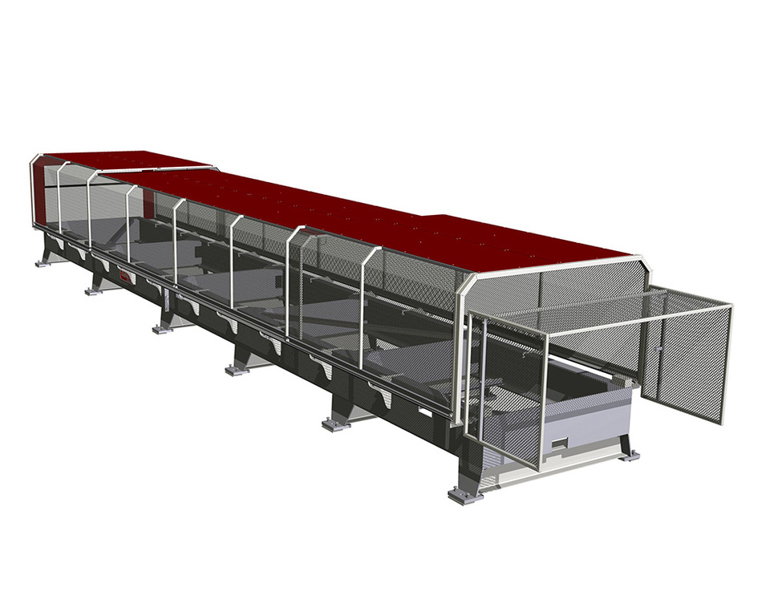
- Fixed transmission and pinch point guarding and full-length light curtain mounted horizontally on the operator's side at lower leg height.
- All moveable guards are complete with integrated safety switches.
- Fence guarding can be supplied by Hayes once a final factory layout is completed, if manufacturing your own fencing provisions have been made in the safety software for additional safety switches.
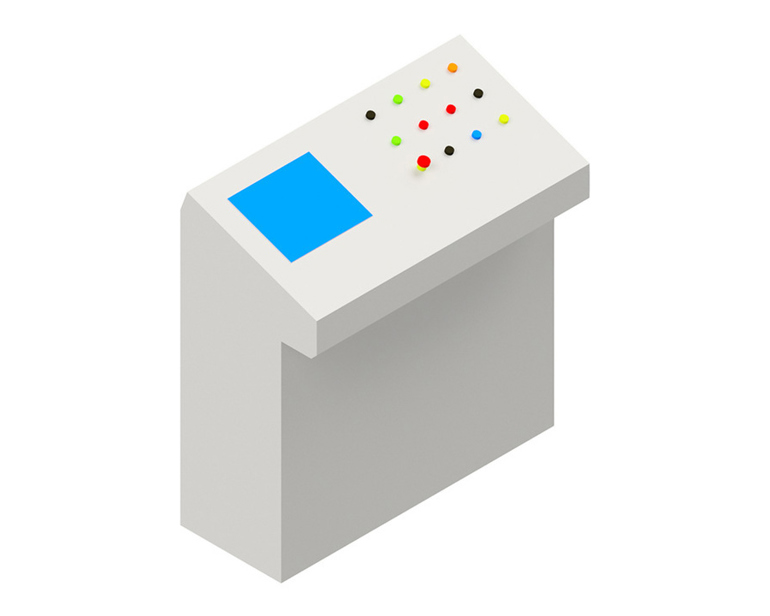
- Standalone operators console with a PC and graphic display used for order entry and programming.
- Provided with Hayes International proprietary software, fully featured with a user-friendly interface and multiple production-saving features.
- Graphic display shows hole position relationships as well as order progress and status.
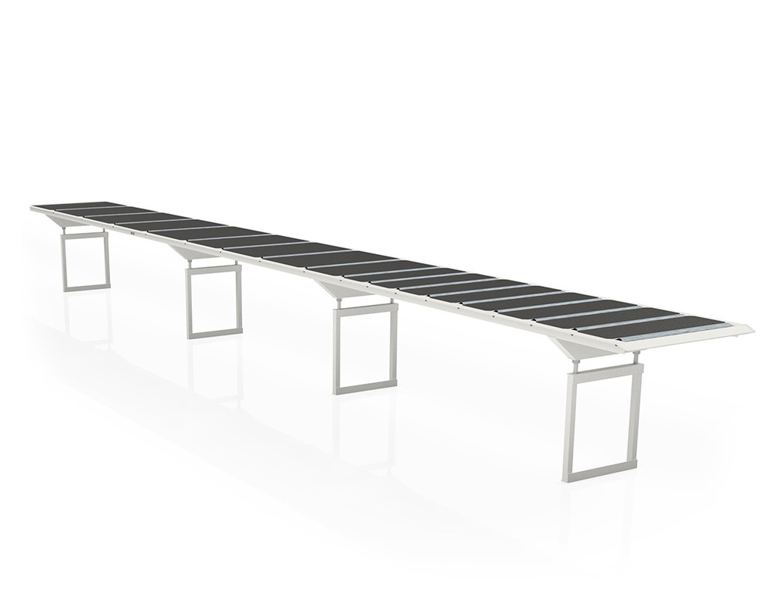
- Height adjustable exit table 11.5-meter length.
- Steel roller supports.
- Lift-up section allows for access to opposite machine side, gate is paired with safety switch that stops machine when gate is open.
Request A Quote
If you’re ready to take the next step, let us know below. One of our team can get in touch to talk through your project. If you’d like to share a drawing, attach it below. We look forward to receiving your enquiry.